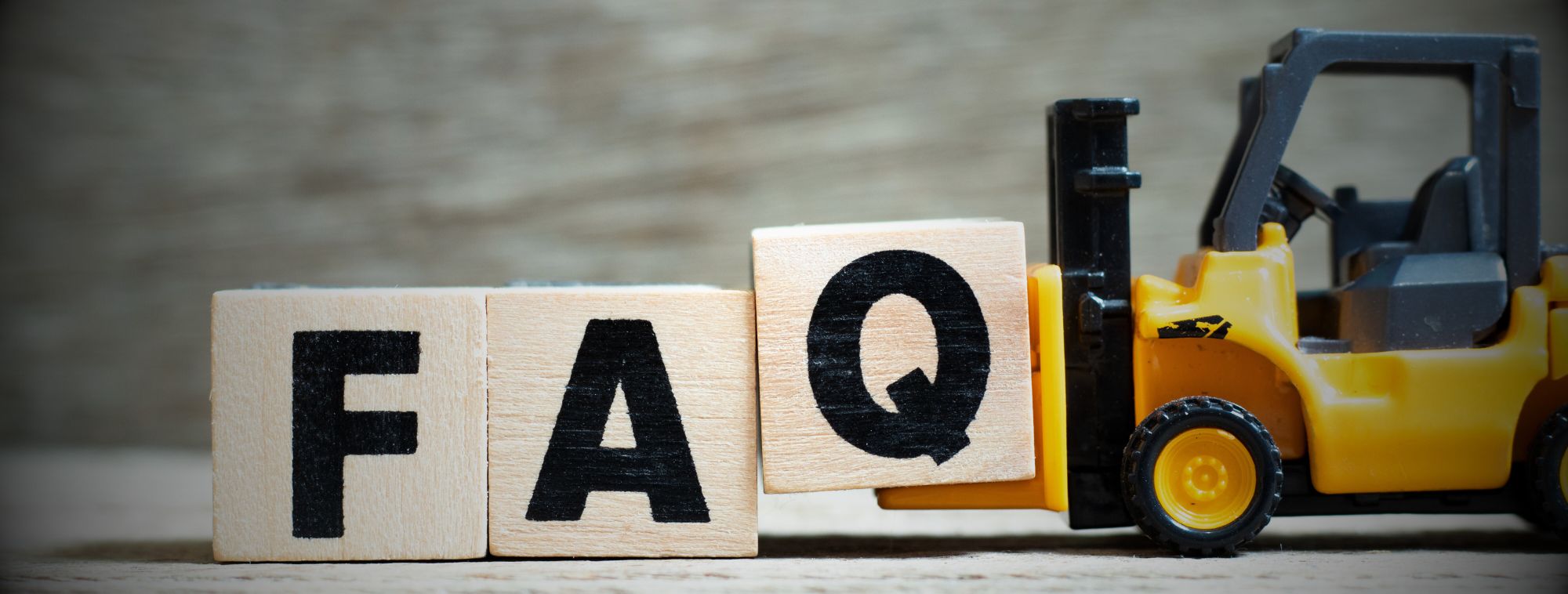
FAQ
Wir sind ein mittelständisches, inhabergeführtes Unternehmen mit ca. 130 Mitarbeitenden. An unserem Hauptsitz Emsdetten sind wir im Maschinenbau tätig und entwickeln Anlagen für Oberflächentechnik, während unserer Werk in Mühlau bei Chemnitz als Dienstleister im Bereich Lohnstrahlen, Beschichtung und Korrosionsschutz tätig ist.
Wir entwickeln und bauen Oberflächentechnik bis hin zu kompletten Oberflächenzentren. Jede Anlage wird maßgeschneidert auf die Bedürfnisse des jeweiligen Kunden geplant und optimal in den vorhandenen Produktionsprozess integriert. Dabei erhalten Kunden bei uns das gesamte Spektrum der Anlagentechnik “aus einer Hand”, z.B.
- Vorbehandlungsanlagen
- HD-Waschkabinen
- Prozesswasseraufbereitungsanlagen
- Strahlkabinen, Strahlhallen
- Zinkspritzanlagen
- Druckstrahlautomaten
- Lackierkabinen, Lackierhallen
- Freiflächenlackieranlagen
- Pulverbeschichtungsanlagen
- Teleskoptrockner
- Fördertechnik
- Hubarbeitsbühnen
Im Werk Mühlau bei Chemnitz bieten wir folgende Strahlarbeiten an:
- Entgraten (Entfernen von Graten und scharfen Kanten an metallischen Werkstücken)
- Reinigen (Entfernen von Rost, Zunder und anderen Verunreinigungen)
- Shot Peening (Gezielte Oberflächenbehandlung zur Erhöhung der Lebensdauer von Bauteilen durch Oberflächenhärtung)
- Sandentfernung (Entfernen von Sand, insbesondere bei Gussteilen)
- Entschichten (Entfernen von alten Beschichtungen, z.B. vor dem erneuten Lackieren)